Getting Welding Excellence: Revealing the Keys of WPS Execution and Optimization
In the world of welding, attaining excellence is a pursuit that depends upon the precise execution and optimization of Welding Treatment Requirements (WPS) These fundamental documents offer as the foundation of welding procedures, dictating the treatments and parameters needed for generating premium welds consistently. Nevertheless, the keys to opening the complete capacity of WPS exist not just in understanding its importance but likewise in understanding the complexities of its application and optimization. By diving into the crucial components, strategies, difficulties, and best practices linked with WPS, a globe of welding quality awaits those who agree to explore its midsts.
Significance of WPS in Welding
The Significance of Welding Treatment Specs (WPS) in the welding sector can not be overemphasized, working as the foundation for ensuring consistency, quality, and safety in welding operations. A WPS provides comprehensive instructions on exactly how welding is to be carried out, consisting of crucial variables such as products, welding processes, joint design, filler steels, preheat and interpass temperature levels, welding currents, voltages, travel speeds, and extra. By adhering to a distinct WPS, welders can keep uniformity in their work, bring about consistent weld high quality across various projects.
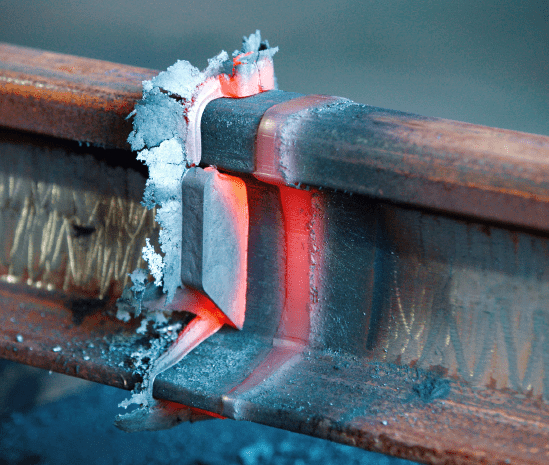
Crucial Element of WPS
Reviewing the integral parts of a welding procedure spec (WPS) is essential for comprehending its role in welding operations. One crucial element of a WPS is the welding procedure spec, which lays out the particular welding processes to be used, such as gas tungsten arc welding (GTAW) or protected metal arc welding (SMAW) By including these essential components right into the WPS, welding treatments can be standard, guaranteeing top quality, performance, and safety in welding procedures.
Methods for WPS Optimization
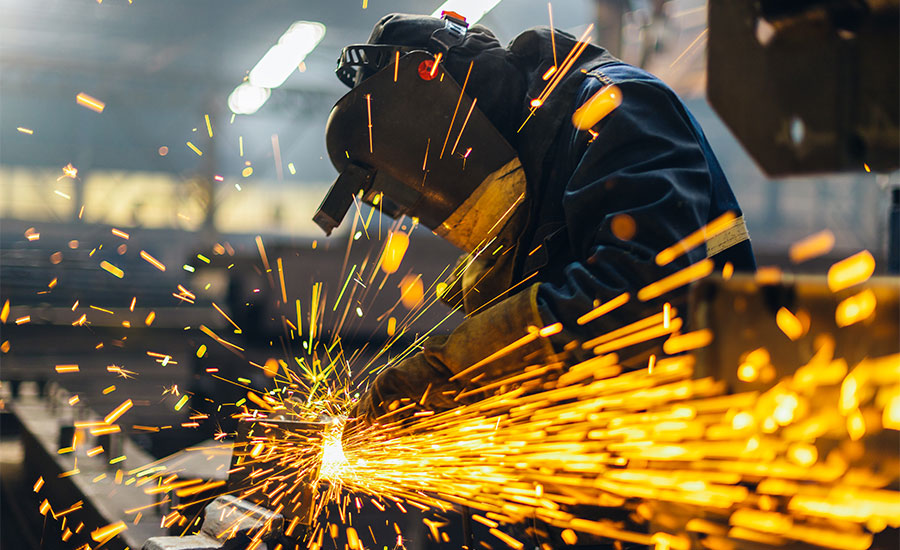
Secondly, training and certification of welding employees according to the particular demands of the WPS is paramount. Supplying thorough training programs and ensuring that welders are licensed to perform treatments laid out in the WPS can bring about higher quality welds and decreased rework.
Furthermore, leveraging modern technology such as welding software program and surveillance systems can aid in optimizing WPS. These tools can assist in tracking variables, guaranteeing specifications are within specified limitations, and supplying real-time comments to welders, allowing them to make instant modifications for enhanced weld high quality.
Typical Difficulties and Solutions
Encountering challenges in executing the methods for WPS optimization can impede welding operations' performance and top quality. One common obstacle is insufficient training or understanding of the welding procedure specifications (WPS) amongst the welding group.
An additional difficulty is the lack of correct paperwork and record-keeping, which is crucial for WPS optimization. Without clear documents of welding parameters, products utilized, and evaluation results, it comes to be difficult to identify locations for improvement and make certain consistency in welding procedures. Carrying out a robust documents system, such as digital welding monitoring software, can assist streamline record-keeping and assist in data evaluation for continuous renovation.
Additionally, irregular welding equipment calibration and upkeep can pose a substantial challenge to WPS optimization. Normal equipment checks, calibration, and maintenance timetables ought to be stuck to strictly to ensure that welding parameters are precisely controlled and preserved within the defined Visit Your URL tolerances (welding WPS). By attending to these usual difficulties with aggressive services, welding procedures can enhance efficiency, top quality, and overall welding excellence
Finest Practices for WPS Application
To ensure effective WPS implementation in welding operations, adherence to market criteria and meticulous interest to information are paramount. When initiating WPS application, it is critical to start by completely recognizing the details welding requirements of the task. This requires a comprehensive evaluation of the welding procedure specs, products to be welded, and the environmental conditions in which the welding will occur.
As soon as the needs are clear, the following action is to pick the ideal welding procedure that aligns with these specs. This entails getting in touch with the pertinent codes and criteria, such as those provided by the American Welding Society (AWS) or the International Organization for Standardization (ISO), to ensure compliance and top quality.
In addition, documenting the entire WPS execution procedure is vital for traceability and quality assurance. Thorough records need to be kept relating to welding parameters, material preparation, preheat and interpass temperatures, welding consumables utilized, and any type of deviations from the initial treatment. Regular audits and evaluations of the WPS can assist determine locations for enhancement and make sure recurring optimization of the welding procedure.
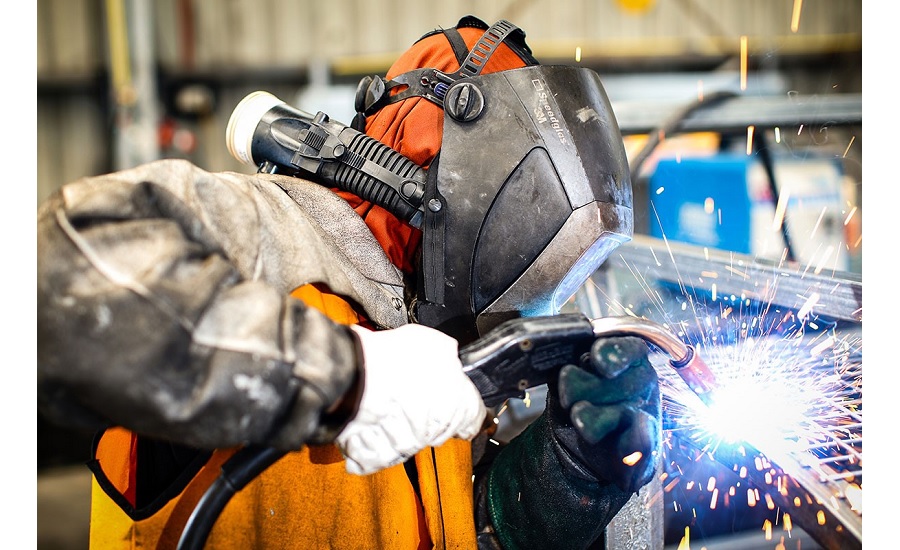
Conclusion
Finally, the application and optimization of Welding Treatment Specs (WPS) is crucial for accomplishing welding excellence. By comprehending the crucial elements of WPS, implementing reliable strategies for optimization, resolving common difficulties, and following finest techniques, welders can guarantee high-grade welds and risk-free working problems. It image source is essential for experts in the welding market to prioritize the proper implementation of WPS to improve general welding efficiency and attain desired results.
The Relevance of Welding Procedure Specs (WPS) in the welding sector can not be overstated, serving as the foundation for making certain consistency, high quality, and safety and security in welding procedures. A WPS gives detailed directions on exactly how welding is to be carried out, consisting of essential variables such as materials, learn this here now welding processes, joint style, filler steels, interpass and preheat temperature levels, welding currents, voltages, travel rates, and a lot more. One vital element of a WPS is the welding process requirements, which lays out the details welding processes to be utilized, such as gas tungsten arc welding (GTAW) or protected metal arc welding (SMAW) By incorporating these key components right into the WPS, welding procedures can be standardized, ensuring quality, efficiency, and security in welding operations.
It is crucial for specialists in the welding sector to focus on the correct execution of WPS to improve overall welding efficiency and accomplish desired end results.
Comments on “Producing a Welding WPS: Step-by-Step Recommendations for Professionals”